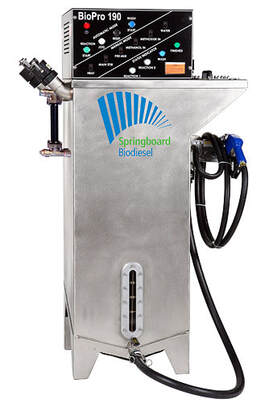
The BioPro™ 190 and The BioPro™ 190EX convert plant or animal oil feed stocks into biodiesel. Biodiesel burns significantly cleaner than diesel fuel – up to 90% less CO2 per gallon and 50% less particulate matter – and can be used to fuel any diesel engine with no need to adapt or modify it.
One unique aspect of the BioPro™ is its automation. The BioPro™ works a lot like a breadmaker – put in the right ingredients and then leave it to handle the various necessary tasks. Very little user interaction (or time) is needed. Instead of having to turn valves, meter in chemicals, and carefully monitor and advance the process, the BioPro™ user simply loads the ingredients and then leaves the machine to its work.
Ingredients
The BioPro™ utilizes two chemical processes – acid catalyzed esterification and base catalyzed transesterification, followed by washing and drying cycles, to make the biodiesel fuel. The ingredients used are feed stock, methanol, acid and base catalysts, and water.
Before starting the process, the user fills the main compartment of the TIG welded 304 stainless steel tank up to the large “FILL LINE” marker (indicating 50 gallons) with filtered, de-watered feed stock. If necessary, the BioPro™ can also de-water the feed stock. The feed stock can be virtually any type fat or oil of animal or plant origin. (Mineral oils, such as used motor oil, cannot be used.) Recycled cooking oil from restaurant kitchens is the most popular type of feed stock, although any number of fresh animal or plant oils may also be used.
After filling the main chamber with 50 gallons (190 liters) of feed stock, the user adds a predetermined amount of base catalyst and methanol to two other dedicated compartments. The base catalyst can be either sodium hydroxide (caustic soda or lye) or potassium hydroxide (caustic potash). It is weighed with the included scale and then poured into its labeled port using the included catalyst pitcher. (All catalysts can also be purchased in pre-measured doses, eliminating the need to weigh or measure them out.)
The methanol is then added via pumping or pouring to the proper labeled ports, where large, graduated level gauges indicate when the correct amount has been added. The final step is to measure out the small dose of acid catalyst (sulfuric acid), using the included acid beaker. The user then presses the green “START” button and pours the sulfuric acid into its labeled port.
In total, the time spent preparing the BioPro™ to make a 50-gallon batch of fuel is less than 30 minutes, and after pushing “START”, the chemical reactions take place automatically. There is no need to return to or check on the machine. It monitors the status of the process and progresses through the various stages to completion.
Once the BioPro™ is underway, the feed stock is transformed into high quality biodiesel through the following steps:
Reaction 1 – Acid Catalyzed Esterification
This chemical reaction doesn’t actually make much biodiesel. Rather, it significantly reduces the level of free fatty acids in the feed stock. Free fatty acids are molecules that interfere with base catalyzed transesterification (the next step). They occur naturally in small quantities in any feed stock, but they increase rapidly as a feed stock ages or is exposed to high temperatures (like when it’s used for frying). If too many are present, you can’t make biodiesel.
During the course of reaction 1, some of the methanol is used to react with the free fatty acids present in the feed stock. The sulfuric acid serves as a catalyst for this reaction. The reaction is aided by thermostatically controlled heating and vigorous agitation via a stainless propeller.
By employing an acid catalyzed esterification, a much wider range of feed stocks can be accommodated, and the next reaction can produce higher quality biodiesel.
Reaction 2 – Base Catalyzed Transesterification
This chemical reaction is what actually converts feed stock into biodiesel. The remainder of the methanol is used, along with the base catalyst. The BioPro™ has premixed these ingredients while reaction 1 was in progress. It now meters this solution into the feed stock. During transesterification, each large oil molecule is converted into three smaller biodiesel molecules. These are similar in size and structure to regular diesel fuel. As this occurs, a portion of the original oil molecule is replaced by three methanol molecules. These displaced atoms form a glycerol molecule. The thorough agitation and controlled temperature gradients managed by the BioPro™ ensure a very thorough reaction.
Settling Period
After both reactions have taken place, the agitation ceases and the glycerol molecules formed in reaction 2 settle to the bottom of the tank along with other minor bi-products such as soaps and salts. The biodiesel, being less dense, forms a clearly separate layer above this glycerin phase.
Midpoint – Drain Glycerin
At this point, (24 hours after the beginning of the process for a standard BioPro™ 190, or 8 hours for a BioPro™ 190EX) the user comes back to the machine and drains out the settled glycerin through the large drain valve and begins the washing cycle. This is the only user interaction required during the process, and should take less than 5 minutes.
Washing
After the user presses the “WASH” button, the washing processes begin. These processes are necessary to remove trace amounts of glycerin, soaps, salts, methanol, and other contaminants still suspended in the raw biodiesel. Fortunately, all of these contaminants have a strong affinity for water, and so water can be used to strip them out of the biodiesel. The BioPro™ performs three washes.
The first ‘coarse’ wash simply involves a gentle spray of water which picks up contaminants as it sinks through the biodiesel. After the water and contaminants settle to the bottom (water is denser than biodiesel), the BioPro™ pumps out the dirty wash water. A custom sensor distinguishes the difference between the wash water and biodiesel so that no biodiesel is lost.
The second and third washes ‘scrub’ the fuel, so to speak. After the BioPro™ pumps in an appropriate quantity of wash water, the propeller agitates the contents of the tank, thoroughly mixing the biodiesel and wash water. Once again, the water picks up more contaminants and then settles to the bottom, after which it is pumped out. This agitated wash occurs a third time, after which virtually no contaminants remain.
Drying
This is the final step. After all the wash water has been pumped out, some water still remains, dissolved in the biodiesel. Through heating, agitation, and a strategically placed evacuation fan, water vapor evaporates into passing air, thoroughly drying the biodiesel.
Fueling
The BioPro™ is now full of clean biodiesel, ready for use in any diesel engine. So long as the ingredients used were of sufficient purity, this biodiesel will comply with the ASTM D6751 standard for biodiesel fuel quality. Using the included fuel pump and auto-shutoff fueling nozzle, filling up is just like at a gas station, and a lot cheaper.