WHY USE A DRYWASH SYSTEM?
A drywash system is typically a much faster way to purify fuel than a water wash. For instance, the BioPro processors allow 24 hours for the following water wash processes: 1 spray wash, 2 turbulent washes, evaporative drying. (Other processors may advertise faster water washes, but these are typical inadequate and do not include necessary steps, such as drying the fuel.) By contrast, the SpringPro T76 is sized for a throughput of 20 gallons/hour, meaning that a BioPro™ 190’s fuel can be purified in about 2 hours, BioPro™ 190’s fuel can be purified in about 2.5 hours, and a BioPro™ 380’s fuel can be purified in about 5 hours.
Secondly, because a drywash system does not use water, there is no waste water to deal with. This may or may not be a big issue, depending on the user’s location and local regulations. For users in locations where waste water disposal is very tightly controlled, though, water washing of biodiesel may be a thorny issue.
Finally, water washing becomes more problematic as the temperature drops. Emulsions form more easily, and many find it to be impractical during the colder months of the year. A drywash system is inherently free of emulsions and many of the other complications that can arise from water washing in colder weather; thus a drywash system can typically lengthen the ‘brewing season’ for small scale biodiesel producers.
HOW DOES THE SPRINGPRO T76 WORK?
After the glycerin settles and is removed from a user’s reactor (either a BioPro™ or a different system), the raw fuel is pumped out of the reactor, into the SpringPro T76 inlet port. The fuel passes through the drywash media in the lead and lag columns, and exits the outlet port. That’s all there is to it.
HOW IS THE SPRINGPRO T76 SIMILAR AND DIFFERENT FROM OTHER DRYWASH SYSTEMS?
All drywash systems are similar in that they are simply a platform with which to employ some kind of existing drywash media. Some of the leading providers of drywash media include DW-R10, Amberlite, Purolite, Thermax, Eco2Pure and BD-Zorb X. Eco2Pure and BD-Zorb X are absorbent types of media, meaning that they basically ‘soak up’ some of the coarse contaminants in biodiesel. DW-R10, Amberlite, Purolite, and Thermax are ion exchange resins, meaning that they chemically attract and bond to biodiesel contaminants. Almost all drywash systems on the market today use these or similar media. The drywash media is what actually performs the task of purifying the fuel. The SpringPro T76 is compatible with all of the drywash media listed above, although the recommended configuration is a lead column filled with BD-Zorb X and a lag column filled with DW-R10.
Where drywash systems differ is in their configuration and construction. Per the media manufacturer’s specifications, the column in which the drywash media is contained will have a particular aspect ratio and flow-through rate. Any reputable maker of a drywash system will adhere to these, in order to get the best performance from the drywash media. Additionally, any quality drywash system will employ a lead/lag setup, to ensure complete purification and extend drywash media life.
One commonly overlooked aspect of column construction is the support bed for the media. The media must rest on a fine screen to allow the fluid to flow through while keeping the media in the column. One ‘shortcut’ in construction is to simply rest this screen on the bottom exit port of the column. By so doing, media effectiveness and life is reduced because flow near the bottom end of the column must become non-uniform in order to exit. Properly constructed columns use a media bed screen that is elevated slightly above the exit port. This allows the fluid to flow uniformly through the screen, and then to flow toward the exit port. The SpringPro T76 incorporates all of the above appropriate features.
Beyond this, though there is a great deal of variance in quality and ease of use. For instance, the materials of construction are important. Quality drywash columns should be made from steel, not PVC or some other low quality material. The SpringPro T76 is made from steel with a durable powder-coated finish.
Additionally, there is actually a fair amount of plumbing involved in a lead/lag system. There should be at least six valves – one valve entering the system, one valve exiting the system, and a valve at the top and bottom of each column. Brass valves are commonly used, as they are relatively cheap, but brass and other red metals are incompatible with biodiesel over the long term. The SpringPro T76 uses nickel plated valves for long-term durability. The system plumbing is also important. Biodiesel compatible hoses must be used. Hoses that degrade chemically or are not sufficiently robust mechanically can cause an ENORMOUS mess for the user. The SpringPro T76 does not skimp here – only Teflon hoses with braided stainless steel jacketing are used, the hose terminations are JIC hydraulic fittings. These ensure total chemical compatibility as well as unmatched durability and resistance to abrasion or impact. One of the most common causes of plumbing failures on drywash systems is tripping over or snagging on dangling, exposed plumbing. To promote a clean, safe work environment, the SpringPro T76’s plumbing is neat and trim, some of it actually being routed internally through the column support stand.
Eventually, the media in a drywash system will become exhausted. The replacement of the media is an afterthought on many drywash systems. Not on the SpringPro T76. Using the patent-pending Theta-Lok system, each column can independently tilt 40 degrees, elevating the bottom cover and offering easy access for its removal. Spent resin then has a clear, straight exit path into the user’s catch vessel (a large, double lined garbage bag works well.) In contrast, media changes with other systems can be a nightmare. Systems with side ports are fairly easy to work with, but they have a couple of common weaknesses. First, the side ports generally do not project out very far from the column. As a result, when removing the spent media, it can be difficult to keep all of the media which is flowing out of the port directed into the waiting catch vessel (in this case, the garbage bag is pretty much the only option). More often than not, a lot of biodiesel-soaked media ends up on the bottom of the column and on the floor. Additionally, since the media has to go around a sharp corner to drain, it will typically not drain completely, requiring the user to ‘shovel out’ whatever media is left. This is a particular hassle with some absorbent media, as they can get fairly packed inside the columns and do not flow very freely. Systems with end ports (either top or bottom) typically require grappling with a very heavy column. A 10” column typically weighs 120 lbs +, when the biodiesel is drained out for a media change, there is still around 60-80 lbs of wet media inside. Thus, this 180-200lb awkwardly shaped column either must be lifted 1-2 feet off the ground and securely suspended there while the media is removed (in the case of a bottom port), or in the case of a top port, it must be first flipped over, then lifted 1-2 feet off the ground and securely suspended there while the media is removed. Neither is a simple task.
Finally, many columns on the market are simply tippy. They are 6’ tall or so, and their base of support is scarcely larger than the column itself. This is an accident waiting to happen. The SpringPro T76 has a 33” square footprint, with leveling pads on each corner, to make sure that everything is stable and safe.
WHY DOES SPRINGBOARD BIODIESEL RECOMMEND THE USE OF BD-ZORB X IN THE LEAD COLUMN AND DW-R10 IN THE LAG COLUMN?
Based on testing, Springboard Biodiesel feels that this is the optimal configuration using the leading drywash media on the market today. One common issue with ion exchange resins is that they can significantly increase the total acid number of the finished fuel. This is because they hydrolyze some of the soaps that they remove, which actually produces free fatty acids that end up back in the biodiesel. The strength of ion exchange resins is that they work very well as polishers – removing the last traces of contaminants in biodiesel.
By positioning a column of BD-Zorb X, an absorbent media, in the lead position, a coarse removal of soaps takes place before the fuel reaches the lag column containing the ion exchange resin (DW-R10). Thus, the total acid number of the fuel stays well within ASTM specifications, as a large portion of the soaps are simply absorbed, rather than hydrolyzed. The ion exchange resin, in turn is able to polish out the trace remnants of contaminants still in the feedstream, yielding fuel that is remarkably clean. A second benefit of this arrangement is recognized from a cost standpoint. The BD-Zorb X, which bears the brunt of the contaminants in the feedstream, is cheaper to replace than typical ion exchange resins. So the life of the more expensive ion exchange resin is extended by the presence of the BD-Zorb X in the lead column.
WILL FUEL THAT IS SENT THROUGH THE SPRINGPRO T76 MEET ASTM SPECIFICATIONS?
This depends on several factors, not all of which have anything to do with the drywash system. For instance, the total bound glycerin present in the fuel is totally a function of the reactor, not the drywash. The function of the drywash is strictly to remove contaminants (soaps, trace glycerin, residual catalyst, etc.) from fully reacted, unwashed fuel. More specifically, this is a function of the drywash media; the construction of the columns and other components are simply what allow the drywash media to optimally do its job. Under normal circumstances, when used in conjunction with a proper platform (such as the SpringPro T76), the media combination recommended by Springboard Biodiesel has verified the performance claims of the media manufacturers and produced purified biodiesel that easily passes ASTM specifications related to the levels of soaps, trace glycerin, residual catalysts, and other contaminants.
It should also be noted that none of the leading drywash media available today are effective means of removing trace methanol. This is the case in spite of some of the overly optimistic or sometimes downright false claims made by some makers of drywash systems. Typically, unwashed biodiesel may contain 1-1.5% methanol, although this figure can be somewhat higher when certain reaction processes are used. At this methanol level, the fuel will not pass the flashpoints test for ASTM D6751 for biodiesel. The flashpoint will be too low. From a practical standpoint, this should not be a large issue. The fuel will likely need to be treated with more caution, as its flash point will probably be more in the realm of petroleum diesel, and flammability will be more of a concern. If biodiesel made this way is mixed with diesel fuel, the lower flashpoint discrepancy will diminish. A B20 blend of biodiesel (20% biodiesel and 80% diesel fuel) would, for example, have nearly the exact same flash point as regular diesel. Theoretically, the combustion characteristics could be slightly different but we have never seen that occur. Finally, a higher level of methanol present in the fuel could become an issue if it were to chemically degrade any polymer components in the fuel system, however, in our experience, we have never seen an occurrence of this happening with drywashed fuel made in a SpringPro.
WHAT IS THE PROPER WAY TO DISPOSE OF SPENT DRYWASH MEDIA?
Disposal should be per the instructions issued by the manufacturers of the drywash media. To paraphrase, drywash media is typically non-hazardous, solid waste, which can be disposed of like any other solid waste once the biodiesel is drained out.
SHOULD RESIDUAL METHANOL BE REMOVED BEFORE THE FUEL IS SENT THROUGH THE DRYWASH SYSTEM?
No, in fact, it should not be. The drywash media is actually more effective when there is a slight level of residual methanol present. This methanol should be removed after drywashing.
WHAT IS THE LIFESPAN OF THE DRYWASH MEDIA?
This depends largely on the levels of contaminants that must be removed from the biodiesel. The various drywash media manufacturers each publish their own specs on expected media lifespan. Under normal conditions, in the 10” columns on the SpringPro T76, the makers of BD-Zorb X claim a life of around 1400-1700 gallons, and the makers of DW-R10 claim a life of around 11,000 gallons
IS THE “OUT-OF-THE-BOX” OPTION WORTHWHILE WHEN PURCHASING A SPRINGPRO T76? IF SO, WHY?
The “out-of-the-box” option basically spares the user the task of ‘breaking in’ the drywash media in his SpringPro T76. Most drywash media require some procedures when they are first put into service. This can be performed by the customer, and their owner’s manual will describe to them how this is done. Many customers, however, will likely find it worthwhile to have Springboard Biodiesel perform these procedures initially, especially since at this point the customer will have the lowest level of experience/familiarity with drywash media.
Absorbent media, such as BD-Zorb X, often has significant levels of dust when it is brand new. This dust must be washed out of the media using clean biodiesel. This biodiesel can then be used in an engine only after passing through a 1 micron strainer. It typically takes around 50 gallons of clean biodiesel to thoroughly wash the dust out of a 10” column of BD-Zorb X.
Ion exchange resins, such as DW-R10, Thermax or Purolite, must typically be backflushed with clean biodiesel, and then left for 24 hours. Following this, about 50 gallons of clean biodiesel must be flushed through the column to prevent noticeable hydrolyzing of clean biodiesel and the inclusion of free SO3- ions in the finished fuel stream. The biodiesel used in this process will then be unsuitable for use in an engine due to elevated levels of acidity. To reduce this acidity, it must be subjected to esterification and/or caustic stripping and a full wash.
The “out-of-the-box” option will spare the user these procedures.
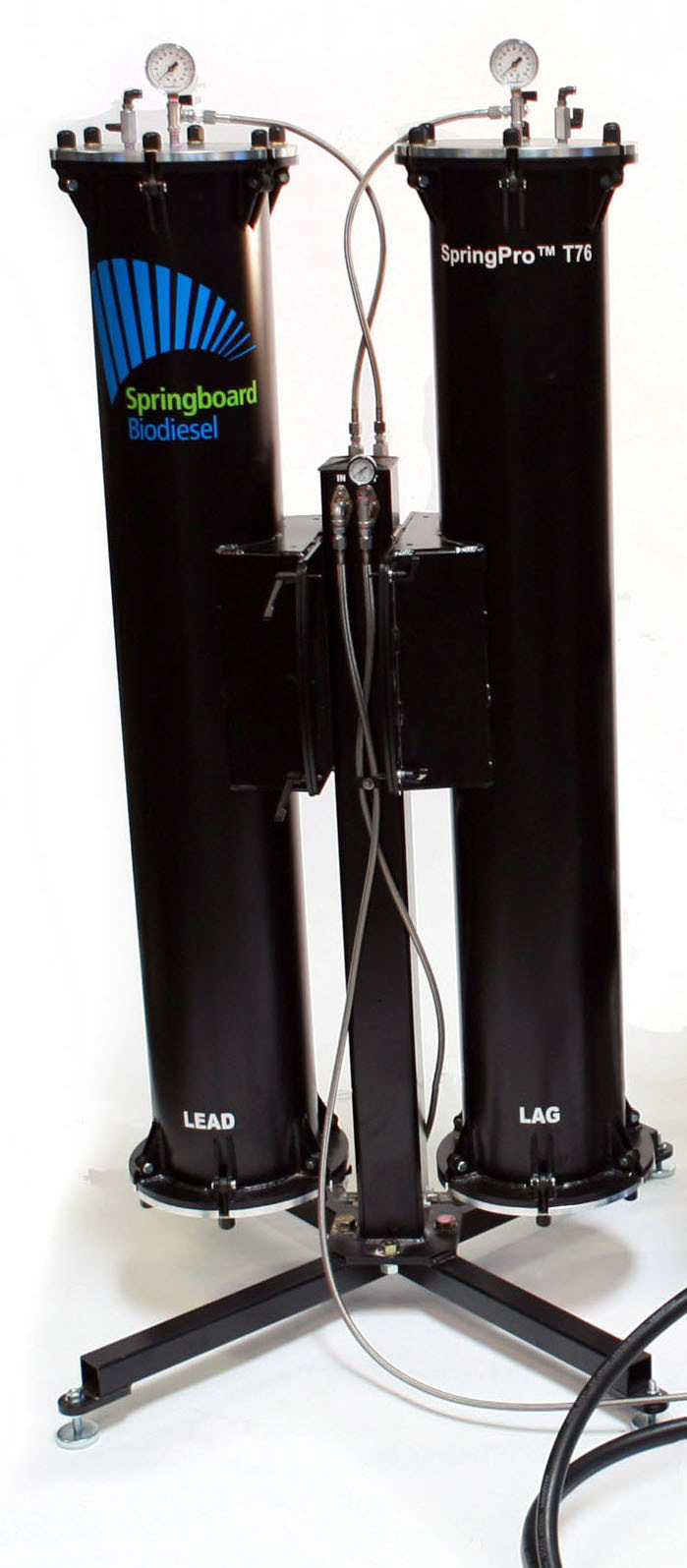