Safety Features
When processing biodiesel, safety must be a priority, not an afterthought. Thus, the design of the BioPro biodiesel processors reflects careful consideration of the safety factors involved. [Video of BioPro safety features]
The primary safety concern associated with biodiesel production arises from the usage of methanol. Methanol’s flash point is 52F and the lower flammability limit is about 6% in air. This calls for appropriate caution when handling.
Although, by comparison, other common fuels, such as gasoline, with a flash point of –40F and a lower flammability limit of only 1.7% in air are much more highly volatile.
The selection of stainless steel for the chassis, rather than much cheaper polymers, such as high density polyethylene, was made, in part due to the fact that flammable liquids would be contained in the unit. The stainless chassis has multiple grounds, and thus cannot build a static charge. Additionally, it is much more mechanically robust, and will resist puncture or softening at higher temperatures, which could easily result in a hazardous spill.
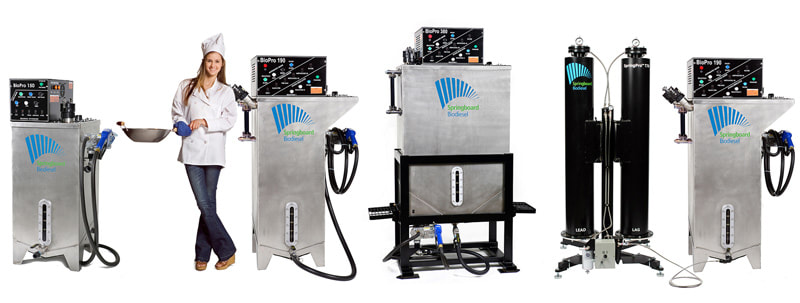
Great care is taken to prevent methanol from leaking inside the lid, where the electrical components are:
- All of the internal hoses are made of stainless steel to prevent any possible puncture and resultant leakage.
- All ports from the lid into the machine tank are sealed. The pump heads which handle the methanol are a diaphragm style, so there is no shaft seal to leak and allow fluid to get to the motor driving the pumps.
- The motor which drives these pumps is also rated as Explosion Proof (Class 1, Division 2).
- The main mixing motor is a C-Face unit, with a shaft and propeller extending into the main tank.
- The face of this motor is sealed against the tank lid, and the motor itself is Explosion Proof (Class 1, Division 2).
- Likewise the methoxide mixing propeller is sealed from the rest of the machine as well, and is driven by an Explosion Proof rated motor.
All electrical devices are listed by UL, CE or another NRTL. Relays coils are ‘ice-cube’ style, sealed in a plastic housing. At all times when the machine has power, the component housing is constantly purged by a 250 CFM rated exhaust fan. This ensures that in the event of a failure/leak of some kind, methanol vapors can never reach a flammable concentration.
The BioPro 190 and BioPro 380 processors bear a CE mark. This means that a conformity assessment has established that the machine complies with all applicable safety, health, and environmental directives, allowing a consumer to use the machine with confidence. Because the temperatures at which biodiesel is produced cause some methanol to be vaporized, these vapors must be anticipated and handled safely. In order to prevent pressurization of the BioPro, the lid which covers the reaction chamber is not locked down, but is rather held down by its own weight – about 10 lbs. for a BioPro 190 lid. This lid seals the reaction chamber up to a pressure of about 0.11 PSIG. Thus, no significant pressure is allowed to build. Conversely, the very slight pressure that does exist prevents any appreciable amount of methanol from escaping during the course of a batch. Therefore, the emissions of methanol vapors are well within air quality guidelines of OSHA or NIOSH, and several orders of magnitude below a flammability threat.
One of the most common causes of accidents and fires when producing biodiesel is heating elements that have gotten too hot, either by a controls failure or by a failure to be immersed in fluid. To eliminate any such threat, the BioPro processors use only indirect heat. The heaters are affixed to the outside of the tank, and the heat conducts through the tank walls to the fluid. Additionally, while immersed heating elements commonly have densities of 30 or more watts per square inch, the BioPro heaters have a large surface area and low watt density – only 5 watts per square inch, making them intrinsically resistant to overheating.